Packaging Printing Methods and Printing Processing Techniques
As a food composite soft packaging manufacturer, printing is a crucial part of our production process.
Having an in-depth understanding of the principles and operational details of each printing process is one of the essential knowledge and skills. The following is a basic introduction to packaging printing methods and printing processing techniques.
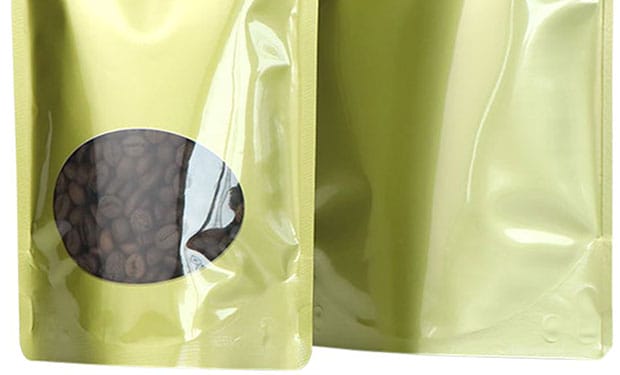
(I) Packaging Printing Methods
1.1. Offset Printing (Lithography)
Offset printing is the most widely used and effective printing method. The printing plate is flat, and it applies the principle of oil and water not mixing.
The non-image areas of the printing plate are composed of a hydrophilic substance, while the image areas are composed of an oleophilic substance. Offset printing is also called lithography.
There are three sets of rollers in the printing process:
- a set of plate cylinders to hold the printing plates,
- a set of rubber cylinders with a special rubber blanket that has good elasticity and flatness,
- a set of impression cylinders. After the plate cylinder is inked, it contacts the rubber cylinder to transfer the image to the rubber.
When the paper enters the machine, it passes between the rubber cylinder and the impression cylinder, and the rubber cylinder transfers the image from the plate to the paper.
Offset printing produces soft tones, exquisite layers, strong three-dimensional effects, convenient plate-making, and seamless printing.
It has a large sheet size, fast printing speed, and low cost. Its disadvantages are that the edges of the printed image are slightly rough, and the ink layer is relatively thin.
For some solid background colors, outlines, and text in offset printing, special color plates need to be made separately and completed by letterpress or flat printing.
1.2. Letterpress Printing
The quality of letterpress printed products is relatively high, with clear graphics and text, distinct outlines without fuzziness, thick ink layers, and bright colors.
Plate-making is convenient. As the oldest printing technique, the principle is very simple, like stamping. The raised parts are inked and directly printed on the substrate.
1.3. Gravure Printing
Gravure printing has a relatively short development history. It reverses the principle of letterpress stamping.
The image areas on the printing plate are recessed below the plate surface, so people call it “intaglio printing”.
Transferring the recessed image to the substrate (paper, plastic, silk) requires a completely new printing process concept. Gravure printing uses web materials for continuous printing.
New gravure presses have very high speeds and are very suitable for large-volume package printing, especially plastic package printing.
1.4. Screen Printing (Silk Screen Printing)
The biggest feature of screen printing is that it can be large or small. The largest screen can print large advertisements, while the smallest can print business cards.
Moreover, it can print on various materials such as paper, cotton, silk, plastic, glass, wood, and metal. In particular, it can print on curved and irregularly shaped objects.
Screen printing, also known as silk screen printing, requires the screen to be made on a mesh.
A photosensitive emulsion is then coated on the mesh, and the prepared artwork or base plate is closely attached to the photosensitive surface for UV exposure.
The exposed parts of the photosensitive emulsion become a waterproof film firmly adhered to the mesh under the action of UV light.
The unexposed emulsion on the screen is washed away with water, revealing the mesh holes that form the image. The prepared screen is fixed on a screen printing machine for printing, or it can be printed using a manual squeegee method.
Each screen represents one color. The number of colors on the design determines the number of screens required. Graduated color printing can also be performed.
The shortcomings of screen printing are that color matching is difficult, the speed is slow, and the production cycle is long for large-volume packaging, resulting in relatively higher costs.
1.5. Digital Printing
Digital printing refers to the process of directly sending electronic files from a computer to a printer, eliminating the time-consuming and costly steps of color separation, film output, imposition, and ink preparation and calibration in traditional printing processes.
It brings printing into the most efficient mode: from input to output, the entire process can be controlled by one person, realizing on-demand printing, especially suitable for printing products with small quantities but many varieties.
Digital printing has developed rapidly due to its flexibility and economy in meeting the requirements of “on-demand printing” characterized by personalized printing, variable data printing, and instant printing.
As a comprehensive technology covering printing, electronics, networks, and communications, digital printing will become a completely new printing model in the future.
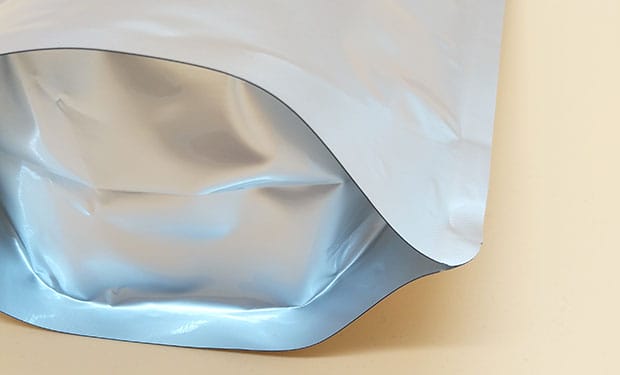
(II) Packaging Printing Processing Techniques
Packaging printing processing techniques are used to improve the appearance and functionality of printed packaging products.
They include varnishing, oiling and polishing, laminating, UV coating, hot stamping, embossing, laser embossing, mounting, die-cutting, and creasing.
2.1. Varnishing
Varnishing is the process of coating (or spraying, printing) a layer of colorless and transparent varnish (varnish oil) on the surface of printed products.
After leveling, drying, and polishing, a thin and uniform transparent glossy layer is formed on the surface of the printed product.
2.2. Oiling and Polishing
Oiling is the process of covering the surface of a printed product with an oil to protect the printed colors.
Currently, commonly used materials include gloss oil (bright oil) and matte oil (dull oil). First, the printed product is oiled, and then it is passed through a polishing machine.
During the transfer process, under the influence of temperature and pressure, the polishing process is completed, thereby improving the gloss and vividness of the surface colors of the printed product and achieving a certain moisture-proof effect.
2.3. Laminating
Laminating is a processing technique that bonds a plastic film to the surface of a paper-based printed substrate through a certain temperature, pressure, and adhesive, forming a paper-plastic composite.
Due to the addition of a thin and transparent plastic film on the surface, it has good gloss, abrasion resistance, and chemical resistance, serving to beautify, moisture-proof, anti-fouling, increase strength, and protect the packaging.
Laminating can be divided into two types: gloss lamination and matte lamination.
2.4. UV Coating
UV coating is the process of evenly coating a layer of UV-curable gloss varnish on the surface of a printed product, followed by UV irradiation to form a cross-linked film through the curing of the varnish.
Areas with UV coating become glossy, creating a textural contrast with areas without UV coating, enhancing the three-dimensional effect of the image.
The advantages of UV varnish are that it can be printed not only on paper but also on plastic, metal, glass, wood, and other materials.
2.5. Hot Stamping
First, the pattern or text to be hot-stamped is made into a relief plate.
With the help of a certain pressure and temperature under the relief plate, the metallized aluminum foil is transferred to the substrate to increase the decorative effect.
It is not only suitable for paper but can also be used on leather, lacquered cloth, wood, silk, cotton, and plastic products. It has the characteristics of bright colors and eye-catching appearance.
2.6. Embossing
Embossing, also known as relief embossing, is a process of creating a raised or recessed image or text on the surface of a printed substrate using pressure without ink.
First, two matching embossing dies, one male and one female, are made.
The paper is placed between the dies, and through pressure, the substrate of the printed product undergoes plastic deformation, revealing a relief effect with varying depths and thicknesses.
2.7. Die-Cutting and Creasing
When a printed packaging box needs to be made into a certain shape, it can be completed through die-cutting and creasing processes.
The process of cutting the substrate into a certain shape on a die-cutting machine using a steel knife (i.e., die-cutting knife) arranged into a die (or a steel plate engraved into a die) is called die-cutting.
The process of pressing a crease or leaving a folding groove on the substrate using a steel wire (i.e., creasing knife) through pressure is called creasing.
In most cases, the die-cutting and creasing processes are often combined in the same die, and die-cutting and creasing are performed simultaneously on the die-cutting machine, so it can be simply called die-cutting and creasing.
It is not only applicable to paper but can also be used on leather, plastic, and other materials.